Automatic servo can seamers bring about a remarkable enhancement in both efficiency and precision through several key mechanisms.
The servo technology employed in these machines ensures precise control over the seaming process. This means that the force, speed, and position of the seaming components are accurately managed, resulting in consistently tight and uniform seams. The elimination of variations leads to higher-quality seals and reduces the likelihood of product leakage or spoilage.
In terms of efficiency, the automated nature of these seamers allows for rapid and continuous operation. They can handle a large volume of cans in a short period, minimizing production time. The seamless integration with production lines ensures a smooth workflow without significant interruptions.
The advanced control systems of automatic servo can seamers enable quick adjustments and optimizations. This means that if there are changes in can specifications or production requirements, the machine can be easily reconfigured to maintain high efficiency and precision.
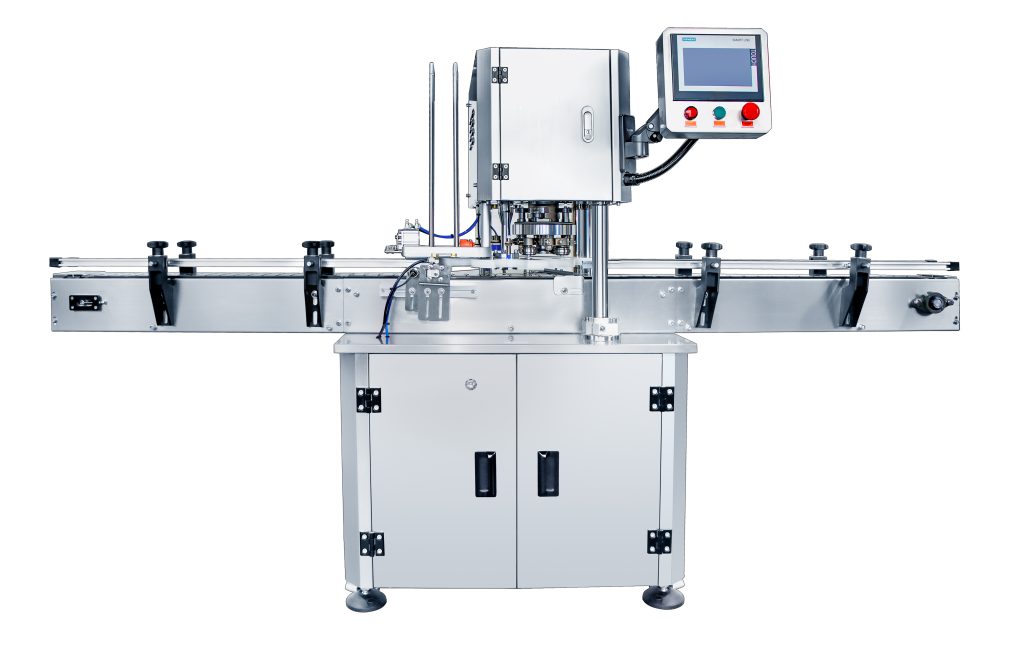
The use of high-quality materials and well-engineered components in these machines contributes to their durability and reliability. This reduces the frequency of breakdowns and maintenance, further enhancing overall productivity.
Additionally, automatic servo can seamers often come with intelligent monitoring and feedback systems. These systems provide real-time data on the seaming process, allowing operators to identify and address any potential issues promptly, preventing delays and maintaining efficiency.
In summary, the combination of precise control, automated operation, adaptability, and reliable components makes automatic servo can seamers indispensable tools for significantly improving efficiency and precision in can seaming processes.