Automatic powder auger fillers bring about a significant improvement in packaging efficiency through several key ways.
Firstly, they offer a substantial increase in the speed of the filling process. With their automated mechanisms and optimized designs, they can fill a large number of containers in a short span of time, allowing for higher throughput and reduced production cycles.
The accuracy and consistency of filling provided by these fillers eliminate the need for rework or corrections. Precise measurements ensure that each container is filled correctly the first time, saving time and resources that would otherwise be spent on addressing filling errors.
The elimination of manual labor in the filling operation reduces human-related delays and inconsistencies. Workers can be redirected to other value-added tasks within the packaging line, enhancing overall productivity.
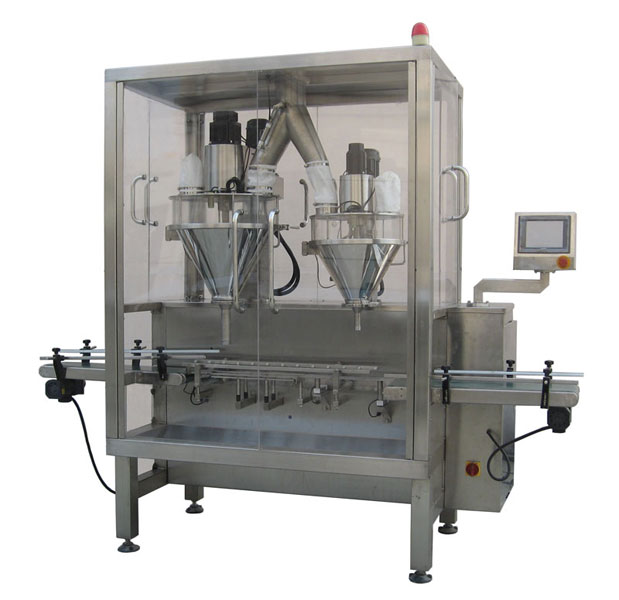
Automatic powder auger fillers are capable of seamless integration with other packaging equipment. This synchronization ensures a smooth and continuous workflow, minimizing downtime and bottlenecks that can occur when different machines operate independently.
The fillers’ advanced control systems and sensors allow for real-time monitoring and adjustment of filling parameters. This enables quick response to any changes in powder characteristics or packaging requirements, maintaining efficiency without significant disruptions.
Furthermore, their consistent performance and reliability mean less frequent breakdowns and maintenance, contributing to uninterrupted packaging operations.
In summary, automatic powder auger fillers enhance packaging efficiency by boosting filling speed, ensuring accuracy, reducing manual effort, integrating smoothly with other equipment, enabling real-time monitoring, and providing reliable operation.